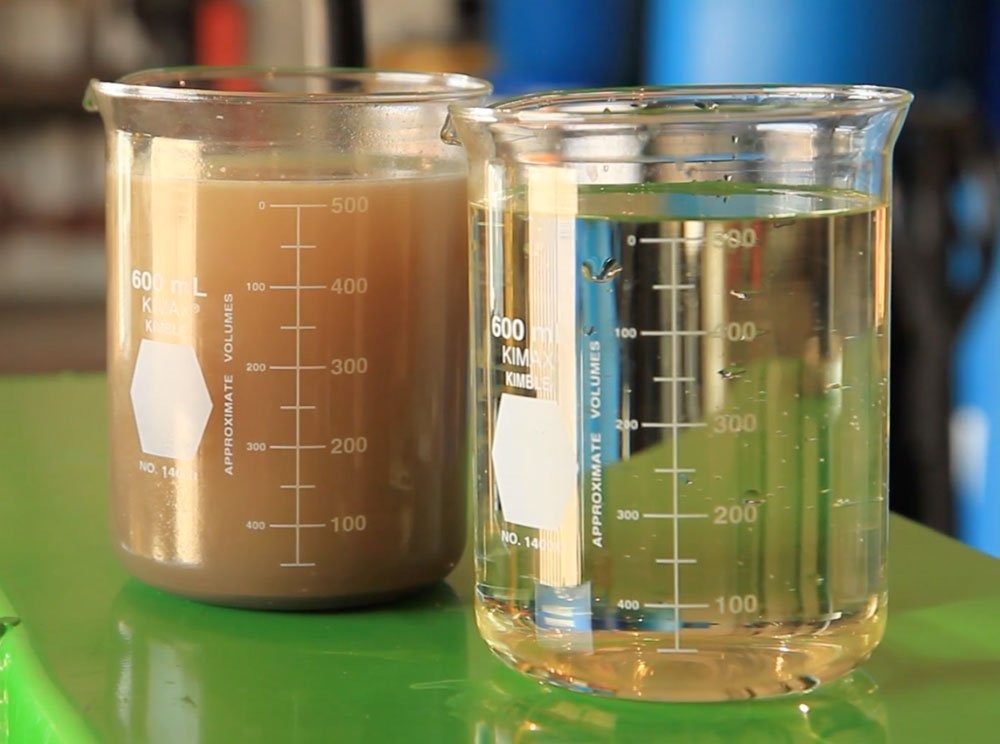
Achieving High-Quality Metal Coatings and The Complex Processes of Nickel and Zinc Plating
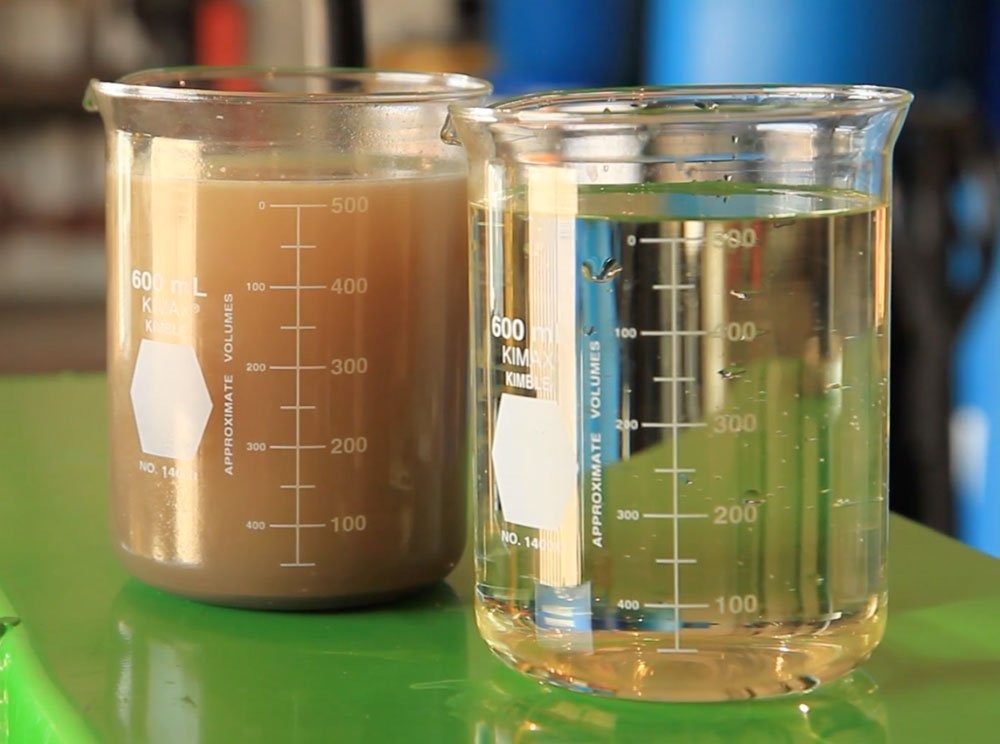
Metal plating, encompassing electroless nickel plating and zinc plating techniques, plays a pivotal role in fortifying the durability, corrosion resistance, and overall quality of metal parts. The pursuit of superior coatings demands a meticulous approach, intricate processes, and a keen understanding of these plating methods, each offering distinct advantages in diverse industries.
Electroless Nickel Plating
Electroless nickel plating, an auto-catalytic process, deposits a uniform layer of nickel-phosphorous or nickel-boron onto metal surfaces. Unlike electroplating, it doesn't rely on electrical currents, ensuring excellent coverage on intricate shapes and internal surfaces. This method is favored for components needing exceptional wear resistance, corrosion protection, and uniform coating thickness, finding applications in aerospace, automotive, electronics, and oil & gas industries.
Critical factors influencing the quality involve precise temperature control of the plating bath and the chemical composition. Maintaining optimal temperature is crucial to regulate the deposition rate and ensure uniformity across the part’s surface.
Chemicals like nickel salts, reducing agents (e.g., sodium hypophosphite or dimethylamine borane), and stabilizers facilitate the reduction of nickel ions onto the substrate, resulting in a corrosion-resistant coating.
Laboratory tests evaluating thickness, adhesion, and corrosion resistance are crucial for quality assurance and compliance with industry standards.
Zinc Plating
Zinc plating involves depositing a layer of zinc onto metal surfaces, offering effective corrosion protection. Widely used in automotive, construction, and electronics industries for parts exposed to atmospheric conditions, it provides sacrificial corrosion protection, prolonging component lifespan.
Maintaining optimal bath temperature and regulating electrical current through a DC plating rectifier ensure uniform deposition and adhesion of the zinc coating.
Zinc chloride or zinc sulfate, along with additives enhancing brightness and corrosion resistance, are vital in achieving desired coating characteristics and process stability.
An electric immersion water heater often aids in maintaining the optimal temperature of the plating bath, contributing to consistent and high-quality zinc coatings.
Similar to electroless nickel plating, thorough laboratory testing validates coating thickness, adhesion strength, and corrosion resistance to meet industry standards and intended purposes.
The Significance of Quality Control
High-quality standards in metal plating are imperative to fulfill industry demands. Accurate temperature control, proper chemical compositions, and rigorous testing methodologies are integral for superior coatings.
Experts stress the importance of temperature control for zinc plating's consistency, while studies emphasize comprehensive testing for evaluating electroless nickel coating performance.
Plating chemicals for zinc plating and AC to DC plating rectifier play critical roles in ensuring effective and durable coatings, supported by technology facilitating optimal bath temperature.
Chemical testing labs validate coating quality through stringent procedures, confirming adherence to standards and suitability for applications.
Both electroless nickel plating and zinc plating significantly enhance the endurance and utility of metal components, reliant on precise parameter control, chemical compositions, and rigorous testing protocols for top-notch coatings across diverse industries.
0 Comments Add a Comment?